What is Spherical Lapping?
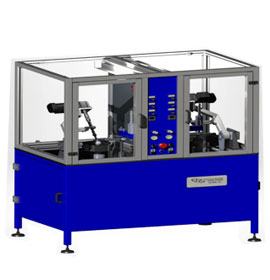
The term "lapping" is used to describe a number of various surface finishing operations where loose abrasive powders are used as the grinding agent at normally low speeds. It is a process reserved for products that demand very tight tolerances of flatness, parallelism, thickness or finish.
How does lapping work?
One or more parts are machined at the same time in a batch process. The abrasive is usually mixed with a liquid vehicle, either oil or water based. The pieces being lapped are captured in retaining rings. Workholders also called "carriers" may be used to keep the parts separated to prevent damage to their edges. The parts are dragged across the lap plate surface on to which the abrasive is being fed.
Lapping is an averaging process where the greatest material removal occurs where the high points of the surface of the part contact the flat lap plate. The object is to produce parts with a uniformly smooth and usually flat surface. A surface that has been lapped exhibits a dull, non-reflective and multi-directional appearance. This condition is referred to as “matte” finish. There may be slight reflectivity on materials lapped with very small micron size aluminum oxide abrasive. This is especially true if the material is relatively hard and the surface roughness measurement is perhaps 5 (.127 micron) micro-inch and below.
Very light “micro-scratches” may be viewed on lapped surfaces. Abrasive of larger micron size and harder compound will generate more micro-scratches in addition to deeper scratches. Most micro-scratches produced with small micron aluminum oxide abrasive will be less than .000001” (.025 micron) deep and can’t usually be measured with a profilometer. Micro-scratches should not be confused with deeper scratches produced by particles of contamination or other causes.
Spherical Lapping vs "Flat" Lapping
The Lapmaster Wolters SPL has been developed to produce a Convex or Concave scratch-free, high quality surface on spherical components. The machine can also match lap a range of mating sphere components such as, Hydraulic timing valves. This system is effective on most materials including ceramic, graphite, ferrous metals, alloyed metals and stellite coatings
The Lapmaster Wolters LBVS has been developed to produce very accurate spherical surfaces on a variety of Ball Valves. A scratch free, matt high-quality surfaces is obtained on the Ball Valve and Seat. The machine match laps two Seats to the valve, achieving a perfect mechanical seal for any pressure requirement.
Why use Lapmaster Spherical Lapping, Grinding and Polishing Machines / Systems?
Lapmaster spherical lapping machines and systems offer a complete line of products for all spherical lapping requirements. We can offer fully integrated systems and machines for high volume spherical lapping and industrial production applications and equipment for low volume job shop applications. Lapmaster also offers used spherical lapping (rebuilt and refurbished) and upgrade services for existing spherical lapping machines. We provide our customers with fully engineered complete custom solutions and offer a full line of accessories and consumables in addition to comprehensive training and repair services.
Our extensive line of spherical lapping machines / systems for both medium to large-scale serial production as well as small batch production; these systems can be made to be manually operated or fully automated. With innovation and customer service as our main objectives, Lapmaster continuously researching and developing new technology and spherical lapping machinery. By consistently staying on top of the latest developments on the market, we ensure that our customers are provided with the most state-of-the-art production and control.