Single & Double Sided Fine Grinding Machinery
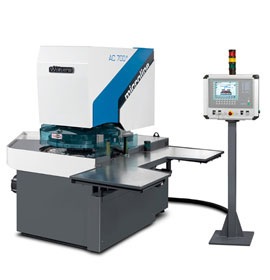
Fine grinding machines, also known as flat honing machines, use technology using fixed abrasive in lieu of loose abrasive for precision finishing. Depending upon the application, fine grinding technology utilizes fixed abrasive diamond or CBN suspended in resin, metal, and vitrified bonds to grind a wide range of materials to very tight specifications. Fine grinding technology uses similar planetary machine designs and kinematics to traditional lapping technology, with several significant advantages.
Fine grinding offers several advantages over the traditional lapping process yet still yielding similar flatness, parallelism, surface finish, and size tolerances. The fine grinding process is much cleaner than lapping, virtually eliminating swarf disposal and work piece cleaning issues. This process is also typically 3-20 times faster than lapping, blurring the lines between traditional lapping and grinding technologies.
LAPMASTER WOLTERS development of fine grinding equipment and processes are bridging the gap between traditional flat lapping and grinding machines, utilizing the best technologies of both. Effective component processing using fine grinding technology requires heavy-duty equipment with sophisticated control systems capable of high plate rotation speeds and down-pressure generation.
LAPMASTER WOLTERS offers several fine grinding machine models, available in both single-sided and double-sided configurations. This line of equipment has been designed using the latest machine construction and control system technology, capable of executing complex grinding routines while producing precise and repeatable results. Full specifications and advantages of LAPMASTER WOLTERS fine grinding equipment are available in individual data sheets.
Compare the advantages:
Traditional Lapping
- Performed with loose abrasive
- Stock removal through abrading action
- Lapped surface is dull and crater-like
- Material and lapping compound are not recycled
- Lapping parts are contaminated and require cleaning
- Slow stock removal rates
Fine Grinding
- Performed with superabrasive solid or pelleted plates
- Stock removal through micro-grooving/cutting
- Fine-ground surface has irregular cross-hatch marks
- Coolant is recycled
- Fine ground parts are coated with thin layer of coolant and if required, only a light cleaning might be needed
- 3-20 times faster than lapping
LAPMASTER WOLTERS offers a full line of fine grinding super-abrasive wheels and dressing stones for all makes and models of fine grinding and flat honing machines. Our wheels incorporate the finest quality and extremely close graded diamond, black CBN and amber CBN in conjunction with our specially formulated vitrified bond. Dressing stones are available to suit all fine grinding wheel formulations and sizes.
Lapmaster Wolters full line of super-abrasive (CBN or Diamond) fine grinding wheels easily adapt to all brands of fine grinding machines and many types of conventional single and double side lapping systems. The fine grinding process produces flat lapping quality on a variety of materials without the expense and "mess" associated with lapping. Fine grinding using Lapmaster supplied fine grinding wheels produces material removal rates up to 20 times faster than lapping. Our special vitrified bond combined with our use of the highest quality most closely graded super abrasive powders means consistent quality for all parts ground on Lapmaster supplied fine grinding wheels.
Vitrified wheels are supplied with configurations comprised of hexagonal pellets applied to steel backup wheels. Pellet type wheels are available with spaces (grooves) between the pellets or with the inter-pellet spaces filled to provide a smooth surface.
Grinding surface pattern, abrasive particle size, bond and thickness of grinding media are all customized for your specific application. Vitrified bonds are the longest lasting and easiest to control for flatness. A variety of wheel diameters are available to suit your single side or double side fine grinding needs. Lapmaster fine grinding technicians are available to determine wheel specifications best suited for your specific application(s).