What is Lapping?
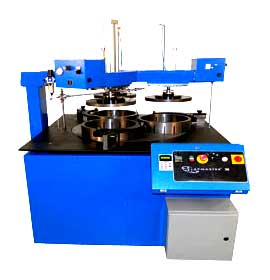
Define Lapping: The term "lapping" is used to describe a number of various surface finishing operations where loose abrasive powders are used as the grinding agent at normally low speeds. It is a process reserved for products that demand very tight tolerances of flatness, parallelism, thickness or finish.
Define Lapping and How it works:
-
Loose Abrasive Process-(LAP)
- Lapping Involves the Use of Abrasive Particles to Modify the Work-Pieces
- The Abrasive Particles are Mixed with a Water-Base or Oil Base Liquid. The Combined Abrasive and Liquid are Called a “Slurry”, this is a Liquid Cutting Tool
- The Slurry is Placed on a Rotating Motorized Platform Called a “Lap Plate”
- The Work-Piece is then Placed Against the Slurry on the Rotating Lap Plate and the Surface of the Work-Piece is Modified
- Rolling/Sliding Action of Abrasive Grains Between Plate and Work piece
How Does Lapping Work?
One or more parts are machined at the same time in a batch process. The abrasive is usually mixed with a liquid vehicle, either oil or water based. The pieces being lapped are captured in retaining rings. Workholders also called "carriers" may be used to keep the parts separated to prevent damage to their edges. The parts are dragged across the lap plate surface on to which the abrasive is being fed.
Lapping is an averaging process where the greatest material removal occurs where the high points of the surface of the part contact the flat lap plate. The object is to produce parts with a uniformly smooth and usually flat surface.A surface that has been lapped exhibits a dull, non-reflective and multi-directional appearance. This condition is referred to as “matte” finish. There may be slight reflectivity on materials lapped with very small micron size aluminum oxide abrasive. This is especially true if the material is relatively hard and the surface roughness measurement is perhaps 5 (.127 micron) micro-inch and below.
Very light “micro-scratches” may be viewed on lapped surfaces. Abrasive of larger micron size and harder compound will generate more micro-scratches in addition to deeper scratches. Most micro-scratches produced with small micron aluminum oxide abrasive will be less than .000001” (.025 micron) deep and can’t usually be measured with a profilometer. Micro-scratches should not be confused with deeper scratches produced by particles of contamination or other causes.
Factors to consider during the Lapping Process
- Type of material being processed
In the years Lapmaster Wolters has been serving industry, customers have asked us to process sample components involving just about every common engineering material known to man and some not so common materials. As our sciences and technologies advance, demands for more precise size tolerances, surface flatness and surface roughness become greater. Many of the technological advances are being derived from the use of new material compounds as well as more exotic natural materials. Lapping and polishing is a machining process that is very gentle and produces low stress levels in delicate and brittle materials. Yet these operations have the capability to process the hardest materials on the face of the earth. A small cross section example of the materials processed on Lapmaster machines is shown below.
- Speed of plate
Depending on the aspect ratio of the component, a lap plate speed must be selected that will not cause the component surface to oscillate, vibrate or depart the lap plate surface in any way. The surface requiring lapping must always register firmly and positively to the lapping or polishing plate surface.
- Pressure on work-piece
The amount of pressure applied to the components being lapped can effect resulting surface roughness by altering the slurry film thickness. The higher the pressure (3 P.S.I. maximum for conventional lapping) the thinner the film thickness and the greater the chance of “wiping” the components against the lap plate. When lapping to achieve fine surface roughness it is recommended to not exceed 2 P.S.I. for most common applications.
- Plate material
- Size and type of abrasive
Abrasive compounds (fused and non-fused Al2O3; black and green SiC, B4C, mono-crystalline diamond and polycrystalline diamond) have crystal structure that determine the hardness, shape, number of cutting edges and friability of the material. Friability is the rating of the crystal bond strength that determines the force required for cleaving cutting edges from the crystal. Under the same conditions of PSI load, harder compounds (ex. SiC) penetrate the component material to a greater depth before edge cleavage than softer compounds (ex. Al2O3) thus generating greater surface texture. Flat hexagonal crystal shape has fewer sharp cutting edges and penetrates or gently shaves the component material less deeply than a blocky tetrahedron shape that gouges chips with a large number of protruding cutting edges. More friable abrasives (ex. Al2O3) require less force to break off cutting edges than less friable abrasives (ex. SiC). Another important factor regarding friability is the size of the crystal reduces as cutting edges break off. As the crystal becomes smaller it cuts smaller chips and generates lower surface roughness measurements.
- Vehicle used & Abrasive to Vehicle Slurry Ratio
The correct ratio must be used when lapping to obtain consistent, repeatable surface roughness. More importantly, the ratio is a factor of film strength and thickness. If the film thickness is too low the component material will tend to wipe closer to the lap plate and greater cutting energy will be transferred through the abrasive particles to the component material causing greater penetration, more severe scratching and higher surface roughness measurements.
- Flatness of plate
An important concept to understand is that the lap plate flatness measured across its diameter doesn’t need to be the same measurement as the component finished flatness specification. This is because the component conforms to a small span of the lap plate geometric spherical radius. The span of the component is its diameter, if circular, or the greatest length across the components lapped surface. In other words, a one inch diameter component will be lapped much flatter than a four inch diameter component when utilizing the same lap plate. The exact flatness required on the lap plate can be mathematically calculated using the trigonometry formula for the determination of cord length.
- Feed system
- Method of charging and conditioning the plate
- Plate temperature
Fundamental Lapping Theory
The basic theory of lapping starts with the components being placed within the confines of conditioning rings directly onto the surface of a rotating lap plate that is coated with a precision film layer of slurry. The components should never come into direct contact with the lap plate surface. Through powered lap plate rotation, the loose and rolling abrasive particles within the slurry layer transfer cutting energy with their sharp cutting edges by penetrating the contact surface of the components removing microscopic chips of material. Concurrently the abrasive is acting on the lap plate via the contact surface of both the components and conditioning rings causing wear that when controlled by adjustable radial ring position will effect spherical curvature changes to maintain a flat lap plate condition.
What Takes Place During The Lapping Process?
- The Surface Finish is modified and is usually improved in surface and sub-surface qualitative values (smoother)
- Geometry (flatness) of the processed surface becomes flat or spherical in contour as a result of Lapping
- Some amount of material is removed from the Lapped surface of the work
The most obvious difference between lapping and the other major machining operations is lapping doesn’t use a single or multiple point cutting tool. Lapping cuts chips by way of a loose abrasive process. One of several different types of precision micro-graded abrasive compound powder is mixed at a specific ratio with cutting fluid and dispensed onto a rotating lap plate.
The compound material, percentage mixture volume, abrasive particle micron size and applied pressure determine the resulting stock removal rate and surface roughness. The mixture of abrasive and cutting fluid is called “slurry” or “lapping slurry”.The difference in the types of abrasives, as well as the size and cost will vary considerably so it is important to know which abrasive best suits your needs. The material to be lapped determines what type of abrasive is used, and the amount of material to be removed together with the specified surface finish governs the abrasive grain size.
For example, extremely hard materials such as sapphire, carbides, and some ceramics require diamond or boron carbide. The medium hard materials, which includes harder metals and some aluminas, can be lapped with silicon carbide. Aluminum oxide is widely used in the glass and silicon industry because of its softer cut and lower cost. Keeping in mind that the abrasive charges the surfaces of your lap plates, it is almost always preferable to have your plates softer than the material being lapped, while the abrasive should be as hard as, or harder than the work pieces.
Lapping Process Basics
- A very passive form of grinding (low pressure, low speed, low removal rate)
- Requires the use of micron-sized Abrasive Particles (not mesh or grit sized abrasive)
- Some amount of movement is required on the part of the tool (lap plate), the workpiece or both
- In most cases, lapping is utilized on flat surfaces, not spherical shapes or contours
- The lap plate is usually softer that the work- piece
- The Conditioning/Retaining Ring is same hardness or harder than the Lap Plate
- Lapping is almost always a “wet process”
- The work-piece never contacts the lap plate
- Only a small amount of material (as little as 5 microns or as much as 500 microns) is removed from each side of the work
- Lapping is always a batch loading process