Flatness Inspection of Lap Plates
What is Lap Plate Flatness Control / Measurement Equipment and how are they used for Lap Plate Flatness Control?
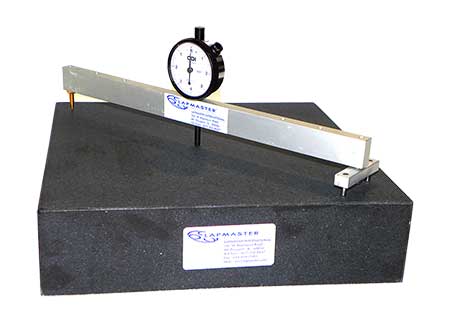
A critical function of operating any lapping or polishing machine, with a plate surface that wears during use, is making machine adjustments to insure the flatness of the components being machined. The only way to obtain a flat component is to make certain the lap plate is correspondingly flat over a distance equal to the maximum span of the component. Additionally it must be understood that the component flatness obtained is a corresponding mirror image of the lap plate over the span of the components lapped surface; a convex plate produces a concave component and vice versa.
The lap plate flatness necessary to achieve a specific flatness on a component is determined by the components engineering flatness specification, maximum span of the component’s lapped surface and diameter of the lap plate.
Straight Edge
A ground steel straight edge is a reference tool commonly used to help measure lap plate flatness. The straight edge possesses a precision beveled, flat ground edge accurate to .0004” maximum flatness deviation per foot of length. The proper measurement technique is to use a straight edge that is the same length as the diameter of the lap plate. The lapping machine must be stopped, two conditioning rings must be removed and a narrow span extending directly across the center of the lap plate diameter must be carefully cleaned. The beveled true side of the straight edge is then placed onto the cleaned span and supported upright while eyesight or feeler gauges are used to measure any existing gap between the plate and the straight edge. A gap at the outside diameter of the lap plate indicates a convex curvature while clearance at the inside diameter denotes a concave curvature.
This lap plate measurement technique is the least accurate, most unproductive and most labor intensive method. No unit of measurement is indicated without the use of feeler gauges and even then the gap distance is only approximate.
Lapmaster provides a straight edge as standard equipment with all single side Lapmaster machines through the model 36. Straight edges can be quoted for machines up to the model 72. It is certainly suggested to recommend the test plug or flatness gauge method on the large machines, a straight edge is too inconvenient and labor intensive for practicality.
Brass Test Plugs
A test plug is simply a specimen of easily machined brass used to help measure the curvature of a lap plate. This technique is the most accurate (resolution of measurement is light bands) and least labor-intensive method of the three common techniques for lap plate flatness measurement. The technique involves lapping the test plug so it possesses the exact curvature of the lap plate except that it is in a mirror image (a convex lap plate generates concave components and vise versa). The most ideal methodology is to lap two test plugs in a conditioning ring with the plugs oriented in a work holder diametrically opposite to each other. This condition allows the plugs to maintain a planetary rotation and thus most accurately measure the true flatness contour of the lap plates entire land area. If a single plug is used it will generally rotate in the conditioning ring on its own axis (no planetary rotation) and only measure the annular track it is occupying on the lap plate land area.
After sufficiently lapping the test plug to the curvature of the lap plate it should be cleaned and polished on a polishing stand equipped with 4/0 emery paper. Four or five strokes on the paper are all that should be required to generate a reflective surface. The paper polish will not alter the plugs lapped flatness because the polishing does not remove enough stock. An optical flat and monochromatic light can then be used to measure the light band flatness of the plug.
Lapmaster offers two sizes of brass test plug, 3” diameter by 2-1/2” high and 6” diameter by 3-1/2” high. Both plugs have a 1/2” through hole machined on center. Brass material is used because it is soft, has sufficient weight to quickly lap, does not cause contamination and scratching; and creates highly visible interference fringe patterns.
Flatness Gauge
A flatness gage is a dial indicator type instrument used to measure lap plate flatness. It consists of a gauge body with two contact feet at one end and one vertically adjustable foot at the opposite end. These three points serve as the reference plane (geometry defines a plane by three points) and a vertical stylus dial indicator measures the lap plates positive or negative deviation from the reference plane. This instrument is very convenient to use and provides a measurement value via the dial indicator. The resolution of the indicator is .0001” units. The use of this gauge involves stopping the machine, removing one conditioning ring and cleaning a linear span of the lap plate from outside diameter to the lap plate counter-bore. The gauge must be calibrated to zero deviation and placed in a radial orientation on the cleaned span of the lap plate. The positive (convex) or negative (concave) flatness deviation is indicated on the gauge.
Lapmaster offers three flatness gauges that are supplied complete with a protective carrying case and hardened, ground, lapped and polished calibration block. The smallest gauge has dual contact foot locations to accommodate the lap plate land distance (4.313” and 4.938”) of the Models 12 and 15, but is also used to measure the Model 20 machine. Another size gauge with a span of 9.328” is available for use on the floor standing models. The last gauge is designed with dual contact point span adjustment (6.812” and 7.312”) for measuring the lap plates of the LSP-6 and LSP-9 dual side lapping machines.
We also offer flatness gages in 12”, 18”, 24”, 32”, 36”, and 48” length with case & granite master.